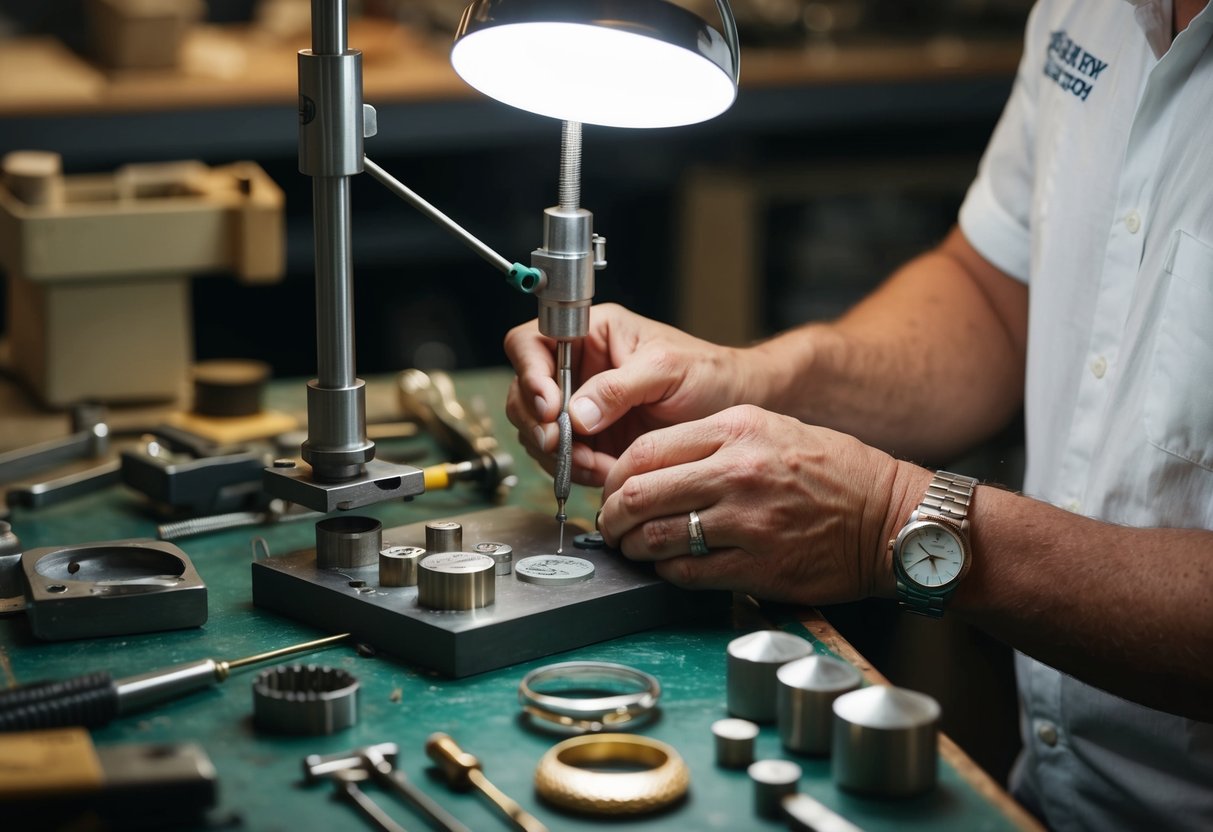
A Comparison of Engraving, Stamping, and Casting for Personalized Jewelry
Check out our personalized jewelry collections! (kids drawing jewelry, coin jewelry, wire jewelry, fingerprint jewelry, handwriting jewelry, and more)
Jewelry personalization is an art that combines sentiment with style. In our constant quest for personal expression, we often turn to specially crafted pieces that speak uniquely to us. Engraving, stamping, and casting each offer distinct benefits and cater to those who seek tailored beauty in their adornments.
Engraving provides intricate detail, allowing for exquisite designs carved with care. Stamping, on the other hand, is ideal for creating straightforward, repeatable patterns efficiently. Casting offers a broader spectrum of shapes and textures, which can result in truly unique pieces.
Determining the best approach depends on individual preferences for customization, durability, and budget. Personal preferences guide us in choosing between these techniques, each bringing its own charm to the jewelry we cherish.
Key Takeaways
- Engraving, stamping, and casting each offer unique personalization benefits.
- Customization is driven by personal preference, durability, and budget.
- Each technique provides distinct charm and personalization options.
Understanding Jewelry Personalization
Personalized jewelry transforms accessory pieces into intimate expressions of individuality. It combines artistic craftsmanship with personal significance, reflecting personal taste and history.
The Art of Making It Personal
Personalization begins with choosing the design that resonates with our story. Whether through inscriptions, symbols, or design elements, these details make each piece unique. Engraving initials or special dates can instantly transform a simple item into a cherished keepsake. We often partner with jewelers to ensure our vision is accurately captured, selecting materials and styles that best suit our personality.
Craftsmanship plays a vital role in personalization. Jewelers employ various techniques like hand-stamping, laser engraving, and custom casting to achieve desired effects. Our engagement allows us to create something truly our own, blending design and emotion into wearable art.
Historical Significance
Throughout history, personalized jewelry has had rich cultural and symbolic roles. Ancient societies used engraved stones and amulets to convey identity and status, turning personal jewelry into more than just decorative items. In the Victorian era, lockets containing photographs or hair became tokens of love and memory, showcasing the enduring appeal of personalized pieces.
This historical perspective shows us how jewelry has long played a part in storytelling. The ability to carry a piece of our history—or our loved ones'—close to us continues to be a compelling reason for seeking personalized jewelry today.
Current Trends in Personalized Jewelry
Modern trends celebrate personalization in innovative ways. We see growing interest in birthstone integration, meaningful charms, and even personalized messages in script fonts. Technology allows for detailed customizations never before possible, including 3D-printed pieces tailored to our exact specifications.
Sustainability also plays a role in current trends. Many seek eco-friendly options, opting for recycled materials or ethically sourced stones. Personalized jewelry, as a reflection of personal values, now frequently aligns with ethical consumption, offering us both beauty and peace of mind.
Engraving Techniques
Engraving offers a versatile method for adding personal touches to jewelry. By selecting the right tools and understanding both the advantages and limitations of engraving, we can create items that hold significant meaning.
Tools and Materials
Various tools are used for engraving, depending on the level of detail desired. Hand-held engravers, like burins and gravers, provide artisans with precision and control over finer details. For larger-scale projects, rotary tools are beneficial due to their ability to carve intricate patterns quickly. Laser engravers stand out for precision and speed, especially in complex designs.
Materials also impact the quality and durability of engraving. Softer metals, such as gold and silver, allow for easy manipulation and detailed work. Harder metals, like titanium, may require specialized tools.
Pros and Cons of Engraving
Engraving provides detailed personalization. The variety of designs achievable by engraving is unparalleled, from names and dates to intricate patterns. This versatility and the permanence of engraving add emotional value to jewelry.
There are limitations to consider. Engraving can be time-consuming, particularly when done manually. Tools and experience needed for quality engraving might also add to the cost. Additionally, once engraved, designs are permanent, which might not suit everyone’s tastes long-term.
Ideal Uses for Engraved Jewelry
Engraving is perfect for personalizing gifts, such as wedding bands and anniversary pieces. It allows us to include meaningful text or patterns, making the item unique. Customizing graduation gifts or commemorating special events with engraved messages also adds a personal touch.
Legacy pieces like heirloom keepsakes benefit from engraving, carrying forward family memories through generations. Engraving wedding sets with initials or special dates also provides a charming way to mark significant life milestones.
Stamping Methods
Stamping involves pressing a design into metal using force, producing consistent and intricate patterns on jewelry. This method integrates both specialized tools and specific techniques, alongside distinct advantages and applications.
Tools and Processes
Stamping Tools: We primarily use metal stamps, which come in various designs, from letters to custom logos. These stamps require a stamping hammer or press for transferring the design onto a metal surface. The metal blank, often silver or gold, is secured on the workbench to ensure precision.
Process: The stamping process is straightforward. We position the stamp accurately on the metal blank, ensuring perfect alignment. Once placed, consistent pressure is applied using a hammer or mechanical press. This action imprints the design deeply into the metal, offering a durable finish.
Benefits and Limitations of Stamping
Benefits: Stamping offers rapid production of designs, making it cost-effective for large orders. The consistency of stamped designs ensures uniformity, which is ideal for producing matching sets. Additionally, the durability of stamped designs stands out, as the imprints resist daily wear.
Limitations: The process can lack flexibility since any revisions require new stamps. The initial tooling costs can also be high, particularly when creating custom stamps for personalized designs. Although ideal for flat surfaces, complex shapes can challenge the stamping process, limiting design options.
Applications for Stamped Jewelry
Applications: Stamped jewelry excels in personalized pieces, such as name necklaces, signet rings, and inspirational bracelets. The ability to replicate exact designs quickly makes it popular in fashion jewelry lines. It's also perfect for customizing charms and pendants, offering a personal touch.
Versatility: Beyond personalization, stamping is advantageous for wedding bands and friendship bracelets, where consistency and durability are prized. Its ability to produce intricate and delicate designs allows it to serve both modern and traditional jewelry styles effectively.
Casting Fundamentals
Casting transforms metal into intricate, detailed jewelry pieces by pouring molten material into custom molds. This method enables designers to achieve complex shapes and textures that other techniques might struggle to capture.
From Mold Making to Metal Pouring
The casting process begins with mold creation. We typically use wax or other materials to craft a detailed model of the desired jewelry piece, which is then encased in a mold material like plaster or silicone. Once the mold sets, we heat the material to remove the wax, leaving a hollow cavity.
Next, we melt the metal of choice — gold, silver, or other alloys — and pour it into the mold. The precision in controlling temperature and timing is crucial to avoid imperfections. After the metal cools, we break the mold to reveal the cast piece, which then undergoes various finishing processes such as polishing and setting gemstones.
Advantages and Drawbacks of Casting
Casting offers us the flexibility to create elaborate and customized designs with incredible detail. It's ideal for producing pieces with complex geometries that would be challenging using other techniques. The ability to duplicate models also makes it cost-effective for batch productions.
Despite its advantages, casting does involve certain limitations. The initial setup, including mold production, can be time-consuming. Additionally, the method requires mastery in temperature control to prevent defects in the final product. This complexity might increase costs for one-time designs.
When to Choose Cast Jewelry
Choosing cast jewelry makes sense when we need to achieve intricate designs and detailed textures. We find it particularly useful for custom pieces where uniqueness and artistry are paramount. This technique is also beneficial when the design involves complex curves or hollow sections.
Casting is favorable for larger production runs due to its ability to replicate pieces accurately. It's an excellent choice for creating heirloom-quality jewelry, where robustness and precision are critical. By understanding the nuances of casting, we can guide our customers to select jewelry pieces that perfectly match their desires and needs.
Comparing Durability and Longevity
When it comes to personalized jewelry, the durability and longevity of different manufacturing techniques play a crucial role in maintaining the beauty and integrity of each piece. The processes of engraving, stamping, and casting offer diverse benefits and considerations regarding wear resistance and maintenance over time.
Wear and Tear Over Time
Engraving provides deep, intricate designs directly on the metal surface. This technique excels in resisting daily wear and maintaining detail. Since engravings are carved into the metal, they are less prone to fading compared to surface treatments. Stamping uses force to imprint designs onto metal. While efficient, stamped patterns may wear down more quickly, especially along edges or raised areas that experience contact.
Casting involves pouring molten metal into a mold to create defined shapes. This method allows for rich detail and smooth surfaces. Cast pieces are generally robust, though intricate designs may be more susceptible to wear in high-contact areas. Each method has unique strengths, and understanding these helps in selecting the right technique for enduring jewelry.
Maintaining Personalized Pieces
To preserve engraved jewelry, regular cleaning with gentle solutions keeps them looking fresh. Our engraved pieces benefit from periodic inspections to ensure that grooves remain defined and free from debris. Stamped jewelry thrives with slightly different care due to its shape. Polishing flat areas helps decrease wear, emphasizing a smooth finish and reducing visible wear on edges.
Cast jewelry requires mindful care due to the intricacy of its designs. Cleaning cast pieces can prevent tarnishing and maintain their luster. While all types of personalized jewelry benefit from regular cleaning, each needs specific attention to retain its unique characteristics and ensure longevity in our collection.
Customization Options Explored
In personalized jewelry, customization involves various techniques to achieve unique designs. The level of detail achievable and the material choices and constraints significantly influence the customization process.
Level of Detail Achievable
When considering engraving, stamping, and casting, each technique offers different levels of detail. Engraving allows for intricate designs and fine details. With tools that trace directly onto the surface, precision is key. Engravings can capture delicate elements like script fonts or detailed patterns effortlessly.
Stamping, in contrast, is best suited for bolder, simpler designs. The method involves pressing shapes into metal with high pressure. This technique cannot achieve the subtleties of engraving. However, it’s excellent for clean and clear lines. Casting, another method, offers a spectrum of detail depending on the mold used. It can range from moderately detailed to more intricate levels, similar to engraving.
Each process dictates the complexity of design we can integrate into our pieces, affecting how personalized a piece can truly be.
Material Choices and Constraints
Materials play a crucial role in customization. Engraving and stamping are traditionally performed on metal surfaces. Gold, silver, and platinum are popular choices for both techniques.
Each metal has unique properties that can affect the outcome. Gold's softness allows for finer engravings, while sturdier metals like platinum endure more forceful stamping.
Casting offers more flexibility in material choice. Apart from metals, materials such as resin or wax can be used. These alternatives allow a broader array of colors and finishes. Yet, different materials introduce varying challenges. For example, the durability and appearance can differ significantly. This requires careful planning for each piece to ensure a satisfactory end product.
Cost Considerations
When creating personalized jewelry, choosing the right technique plays a crucial role in determining costs. We'll explore how each method impacts price points and offer insights into helping you budget strategically for your custom pieces.
Price Points for Each Technique
Engraving generally offers a more affordable entry point. Simple designs are cost-effective and perfect for those seeking personalization without breaking the bank.
Stamping, while slightly more expensive than engraving, shines in its ability to produce well-defined designs efficiently. Aspects such as material type and intricacy influence the final price, leading to moderate cost variations.
Casting, known for its luxurious appeal, is the most expensive technique. It involves creating molds, which adds to production costs. This method suits high-end pieces or intricate designs due to its ability to provide detailed finishes.
Budgeting for Custom Jewelry
Effective budgeting starts with understanding the scope of your project. Materials, design complexity, and production methods will influence costs. Determine your priorities: Do intricate features matter more than material?
Consider material choices carefully. Options like gold or platinum result in higher costs, while silver or brass can offer savings. Align your budget with your design desires to achieve a balanced, personalized piece within your financial limits. Consult with jewelers about potential customizations to get a clear view of pricing before committing.
Turnaround Times
When choosing how to personalize jewelry, turnaround time is crucial. Each method—engraving, stamping, and casting—has its own timeframes. To ensure timely delivery, let's explore production schedules and considerations for special occasions.
Understanding Production Schedules
Production schedules for personalized jewelry depend heavily on the chosen technique. Engraving typically has the shortest turnaround, often completing in a few days. This makes it an excellent option for last-minute gifts.
Stamping generally requires slightly more time, as each piece must be individually crafted. Expect turnaround times in the range of one to two weeks. For pieces requiring detailed designs or special materials, this timeframe could extend further.
Casting often involves the longest preparation period. The process includes creating molds, which can take several weeks to perfect. Plan accordingly if you select this method, as it’s ideal for intricate, high-quality designs but requires patience.
Planning for Special Occasions
For significant events, like weddings or anniversaries, accurate planning ensures your personalized jewelry arrives on time. It's essential to consider the entire turnaround cycle, including both production and shipping times.
Take note that our suggested lead times might vary during peak seasons, such as the holidays when demand surges. Placing your order well in advance guarantees peace of mind and allows us time to address any unforeseen delays.
We recommend contacting us directly to discuss delivery possibilities for any special dates. Adding an extra buffer not only alleviates stress but also provides flexibility for any required adjustments or customizations, ensuring your piece is perfect for your occasion.
Selecting the Right Technique
When choosing a technique for personalized jewelry, multiple factors such as personal style, individual preferences, and experience level with customized pieces should be considered. Each technique offers unique attributes that can significantly impact the final look and feel of the jewelry.
Personal Style and Preferences
Personal style plays a crucial role in deciding between engraving, stamping, and casting. Engraving offers precise and intricate designs, ideal for traditional and elegant tastes. Stamping, on the other hand, exudes a more handmade, rustic appeal, making it a favorite for those who prefer a bohemian or vintage look. Casting provides versatility and can imitate various textures and shapes, catering to contemporary or avant-garde preferences. It’s essential to reflect on the desired aesthetic to select the most fitting technique that resonates with individual style.
Guidance for First-Time Buyers
For first-time buyers, understanding the nuances of each technique is essential to make an informed decision. Engraving typically suits those seeking detailed personalization, while stamping is often more budget-friendly and suitable for simpler designs. Casting is optimal for creative freedom and unique customization needs. We suggest visiting local jewelers to examine samples of each technique. Observing and feeling different pieces can offer valuable insights into what aligns best with personal tastes. Finally, consulting with jewelers can provide tailored advice and help clarify which method best suits your specific requirements.
Frequently Asked Questions
Personalized jewelry is a unique way to express personal style and sentiment. Each technique—engraving, stamping, and casting—offers distinct advantages and characteristics for customization.
How do jewelers achieve personalization through different techniques?
Personalization is achieved through precise application of each technique. Engraving allows for intricate designs and text, while stamping delivers uniform patterns and symbols. Casting provides flexibility in creating custom shapes and forms.
What unique qualities does stamping bring to personalized jewelry pieces?
Stamping offers consistency and repeatability, making it ideal for creating clean and crisp patterns. It's perfect for adding initials, numbers, or symbols, giving a chic yet straightforward look to pieces.
In what ways does casting stand out for custom jewelry designs?
Casting shines with its capability to produce complex shapes and detailed designs. This method is well-suited for bespoke pieces, allowing for a range of creative possibilities that can include 3D elements.
What are the durability considerations when choosing engraving methods for jewelry?
Engraving's durability depends on the depth and precision of the cuts. Deeper engravings tend to be more durable, resisting wear and maintaining clarity over time. It's crucial to consider material hardness when opting for this technique.
How does the jewelry personalization process vary with different materials?
Certain materials respond differently to personalization techniques. Softer metals like gold are more amenable to deep engraving, while harder metals like titanium may suit shallow engraving better. Material choice can influence the technique's effectiveness.
Can personalization details affect the choice between engraving and casting techniques?
Yes, the complexity and detail of personalization often dictate the method. Intricate, detailed work requiring high precision might be better suited for engraving, while elaborate and dimensional designs may benefit from casting.